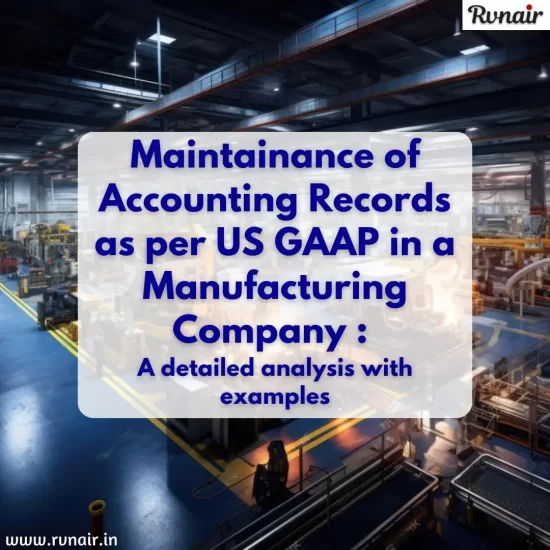
Maintaining accounting records as per US Generally Accepted Accounting Principles (GAAP) in Manufacturing Company involves several detailed steps. These steps ensure accuracy, compliance, and reliability of financial information. Below is an outline of these steps:
1. Establish a Chart of Accounts
- Define Account Categories: Create a comprehensive chart of accounts tailored to the specific needs of a manufacturing company. This should include categories for assets, liabilities, equity, revenues, and expenses.
- Sub-Accounts for Specifics: Sub-divide accounts to reflect specific manufacturing activities, such as raw materials, work-in-progress, finished goods, cost of goods sold (COGS), direct labor, and overhead costs.
2. Implement Robust Internal Controls
- Segregation of Duties: Ensure that responsibilities for authorization, recording, and custody of assets are divided among different individuals to prevent errors and fraud.
- Approval Processes: Establish clear procedures for approving transactions, especially for large expenditures, payroll, and inventory purchases.
- Access Controls: Implement access controls in accounting software to restrict unauthorized access to sensitive financial data.
3. Record Financial Transactions
- Journal Entries: Use double-entry bookkeeping to record all financial transactions in the general ledger through journal entries. Each entry should include a date, description, account names, and amounts.
- Supporting Documentation: Attach supporting documents like invoices, receipts, purchase orders, and contracts to each transaction to ensure traceability and verification.
4. Manage Inventory
- Inventory Tracking: Use perpetual or periodic inventory systems to track raw materials, work-in-progress, and finished goods. Perpetual systems update inventory records in real-time, while periodic systems rely on physical counts.
- Valuation Method: Choose an inventory valuation method (FIFO, LIFO, or weighted average cost) that complies with US GAAP and is suitable for the business model.
- Regular Inventory Counts: Conduct regular physical inventory counts to reconcile with accounting records and identify discrepancies.
5. Cost Accounting
- Direct Costs: Track direct costs such as raw materials and direct labor specifically attributable to the production of components.
- Indirect Costs: Allocate indirect costs (manufacturing overhead) to products using appropriate allocation bases (machine hours, labor hours, etc.).
- Standard Costing: Implement standard costing to compare expected costs against actual costs, facilitating variance analysis.
6. Revenue Recognition
- Identify Contracts: Recognize revenue in accordance with the five-step model of revenue recognition: Identify the contract(s) with a customer.
- Performance Obligations: Identify the performance obligations in the contract.
- Transaction Price: Determine the transaction price.
- Allocation: Allocate the transaction price to the performance obligations in the contract.
- Revenue Recognition: Recognize revenue when (or as) the entity satisfies a performance obligation.
7. Expense Management
- Matching Principle: Ensure that expenses are matched with revenues in the period in which they are incurred to generate accurate financial statements.
- Accruals and Deferrals: Record accruals for incurred expenses not yet paid and deferrals for payments made for future expenses.
8. Payroll Processing
- Accurate Recordkeeping: Maintain detailed records of employee compensation, including wages, salaries, bonuses, and benefits.
- Deductions and Taxes: Calculate and withhold the appropriate amounts for taxes, social security, and other deductions.
- Payroll Liabilities: Record payroll liabilities and ensure timely payment to employees and tax authorities.
9. Fixed Assets Management
- Capitalization Policy: Establish a capitalization threshold to differentiate between capital expenditures and operating expenses.
- Depreciation: Apply appropriate depreciation methods (straight-line, declining balance, units of production) to allocate the cost of fixed assets over their useful lives.
- Asset Tracking: Maintain detailed records of fixed assets, including acquisition cost, depreciation, and disposal.
10. Financial Reporting
- Monthly Closing: Perform monthly closing procedures, including reconciliation of all accounts, to ensure the accuracy of financial data.
- Financial Statements: Prepare financial statements (income statement, balance sheet, cash flow statement, statement of shareholders’ equity) in accordance with US GAAP.
- Disclosure Requirements: Ensure all required disclosures are included in the financial statements, providing full transparency and compliance with US GAAP.
11. Compliance and Audit
- Internal Audits: Conduct regular internal audits to ensure adherence to internal controls and accounting policies.
- External Audits: Prepare for external audits by independent auditors, providing all necessary documentation and explanations.
- Regulatory Compliance: Stay updated on changes in accounting standards and regulatory requirements to ensure ongoing compliance.
Detailed Steps with Examples:
1. Establishing a Chart of Accounts
A well-organized chart of accounts is foundational. For example, accounts for raw materials (1200), work-in-progress (1300), and finished goods (1400) would be created under the inventory category. Expenses might include direct labor (5000), manufacturing overhead (5100), and administrative expenses (5200).
2. Implementing Robust Internal Controls
Example: To prevent fraud, the purchasing department may have the authority to initiate purchase orders, but only the finance department can approve payments. An inventory manager could oversee inventory counts while a separate team reconciles these counts with accounting records.
3. Recording Financial Transactions
When a purchase of raw materials occurs:
- Debit: Inventory (Raw Materials) $10,000
- Credit: Accounts Payable $10,000
Supporting documents like purchase orders and supplier invoices are attached to this journal entry.
4. Managing Inventory
A perpetual inventory system would update inventory records continuously. For instance, each time raw materials are used, the system reduces the raw materials account and increases the work-in-progress account.
5. Cost Accounting
Direct Costs: Track costs like raw materials and direct labor specific to the production of components. Indirect Costs: Allocate manufacturing overhead based on machine hours. If the total overhead is $100,000 and total machine hours are 10,000, the allocation rate is $10 per machine hour.
6. Revenue Recognition
For a contract to supply components:
- Identify Contract: Contract with an automotive manufacturer.
- Performance Obligations: Delivering specific components.
- Transaction Price: $500,000.
- Allocate Price: Entire amount to the delivery of components.
- Recognize Revenue: Recognize revenue upon delivery and acceptance by the customer.
7. Expense Management
Example: If an automotive components production incurs $50,000 in raw material costs and the corresponding revenue is recognized in the same period, the expense is matched to the revenue in the income statement.
8. Payroll Processing
Example: If an employee earns a monthly salary of $4,000, with $500 withheld for taxes and $200 for social security:
- Debit: Salaries Expense $4,000
- Credit: Salaries Payable $3,300
- Credit: Taxes Payable $500
- Credit: Social Security Payable $200
9. Fixed Assets Management
Example: Purchasing a new machine for $100,000 with an expected useful life of 10 years:
- Depreciation Expense (Straight-line): $10,000 per year.
- Entry:
- Debit: Depreciation Expense $10,000
- Credit: Accumulated Depreciation $10,000
10. Financial Reporting
Monthly Closing: Reconcile accounts payable and receivable, perform bank reconciliations, and adjust entries for depreciation and inventory. Financial Statements:
- Income Statement: Revenue from sales of components, minus COGS, and operating expenses.
- Balance Sheet: Inventory, fixed assets, accounts receivable, accounts payable, and equity.
- Cash Flow Statement: Cash flows from operations, investing, and financing activities.
11. Compliance and Audit
Internal Audits: Regularly review transactions and controls to ensure compliance with established policies. External Audits: Prepare detailed schedules and provide documentation for independent auditors to verify the accuracy and compliance of financial statements. Regulatory Compliance: Adhere to standards set by the Financial Accounting Standards Board (FASB) and ensure disclosures meet requirements.
Conclusion
Maintaining accounting records as per US GAAP in an automotive components manufacturing company requires meticulous attention to detail and a robust system of internal controls. By following these detailed steps, the company can ensure accurate financial reporting, regulatory compliance, and effective financial management. This structured approach facilitates transparency, aids in decision-making, and enhances the overall financial health of the organization.