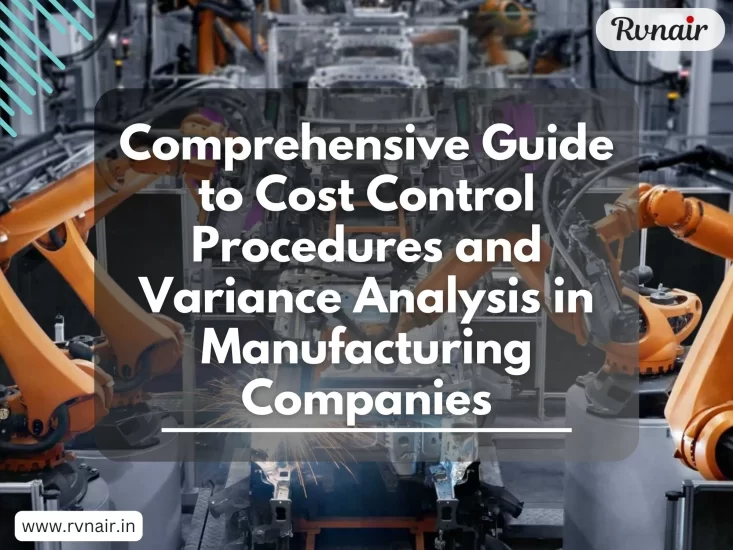
In the dynamic landscape of manufacturing, controlling costs while maintaining operational efficiency is paramount to sustained profitability and competitiveness. This comprehensive guide delves into the intricacies of cost control procedures, the pivotal role of variance analysis, and strategies to address discrepancies in alignment with US GAAP principles.
Section 1: Understanding Cost Control in Manufacturing
1.1 Importance of Cost Control
Cost control ensures that expenses incurred in the production process remain within predefined budgets and standards. This section will explore:
- The strategic significance of cost control in achieving financial objectives.
- How effective cost control contributes to overall operational efficiency and profitability.
1.2 Key Elements of Cost Control Procedures
Effective cost control procedures encompass several essential elements, including:
- Budgeting and Forecasting: Establishing realistic budgets and forecasts based on historical data and market trends.
- Standard Costing: Assigning predetermined costs to materials, labor, and overheads to serve as benchmarks.
- Inventory Management: Optimizing raw material and finished goods inventory levels to minimize carrying costs and obsolescence.
- Performance Measurement: Regularly comparing actual costs with budgeted or standard costs.
1.3 Challenges in Cost Control
Identifying and addressing common challenges faced by manufacturing companies in implementing cost control measures, such as:
- Variability in raw material costs and supply chain disruptions.
- Fluctuations in labor costs and workforce management.
- Overhead costs management and optimization.
Section 2: Variance Analysis: A Strategic Tool for Cost Management
2.1 Understanding Variance Analysis
Variance analysis involves comparing actual costs with budgeted or standard costs to identify discrepancies and their underlying causes. This section will cover:
- Types of variances: Material, labor, and overhead variances.
- Methods of variance calculation and interpretation.
2.2 Importance of Variance Analysis in Manufacturing
Explore why variance analysis is crucial for manufacturing companies:
- Facilitating performance evaluation and decision-making.
- Identifying inefficiencies and areas for cost reduction.
- Enhancing financial transparency and compliance with regulatory standards.
2.3 Techniques and Approaches to Variance Analysis
Detailed examination of various techniques used in variance analysis:
- Direct Material Variance Analysis: Comparing actual material costs with standard costs based on quantity and price variances.
- Labor Efficiency and Rate Variances: Analyzing differences between actual and standard labor costs due to changes in wage rates or productivity.
- Overhead Variances: Evaluating variations in overhead costs attributed to factors such as utilities, maintenance, and depreciation.
Section 3: Resolving Discrepancies and Ensuring Compliance with US GAAP
3.1 Investigating Variances
Upon identifying variances, a systematic investigation is crucial to determine their root causes:
- Conducting root cause analysis and corrective actions.
- Involving cross-functional teams to address production, procurement, and operational issues.
3.2 Adjusting Budgets and Standards
Strategies for adjusting budgets or standards based on validated reasons for variances:
- Revising cost projections and forecasts to reflect current market conditions and operational realities.
- Implementing cost-saving measures and efficiency improvements.
3.3 Compliance with US GAAP Principles
Ensuring all financial adjustments and reporting adhere to US GAAP guidelines:
- Emphasizing principles of consistency, conservatism, and full disclosure.
- Documenting variances and their impacts on financial statements accurately and transparently.
Section 4: Case Studies and Practical Applications
4.1 Real-World Examples
Examining case studies of manufacturing companies implementing effective cost control and variance analysis strategies:
- Lessons learned from successful cost management initiatives.
- Challenges faced and innovative solutions applied.
4.2 Practical Applications
Step-by-step guides and practical tips for implementing cost control procedures and variance analysis in manufacturing:
- Tools and software applications for data analysis and reporting.
- Training and development strategies for enhancing cost management skills among employees.
Section 5: Future Trends and Innovations in Cost Control
5.1 Emerging Technologies
Exploring how advancements in technology are reshaping cost control practices in manufacturing:
- Predictive analytics and machine learning for proactive cost management.
- Internet of Things (IoT) and automation in optimizing production processes and resource allocation.
5.2 Sustainable Cost Control Strategies
Addressing the importance of sustainability and environmental considerations in cost control:
- Green manufacturing practices and their impact on operational costs.
- Regulatory compliance and corporate social responsibility (CSR) initiatives.
Conclusion
In conclusion, effective cost control procedures and variance analysis are indispensable for manufacturing companies striving to achieve financial sustainability and operational excellence. By adhering to US GAAP principles, businesses can enhance financial transparency, mitigate risks, and capitalize on growth opportunities in a competitive global market. Embracing innovative technologies and sustainable practices will further empower organizations to navigate future challenges and drive continuous improvement in cost management.
This comprehensive guide serves as a roadmap for manufacturing executives, financial professionals, and industry stakeholders seeking to optimize cost control strategies and leverage variance analysis for strategic advantage.